Ensuring optimal truck performance is straightforward. It all comes down to scheduled system checks, identifying issues early on, monitoring fleet health, and establishing proactive strategies. Regular inspections and repairs secure reduced interruptions, enhanced performance, and safety. Direction from specialists from experienced technicians will guide you through fleet maintenance through the smart implementation of digital tools, thorough record-keeping, and skilled personnel. Dive into the ultimate guide to fleet maintenance and unlock cost-effective operations. There's so much to discover and understand!
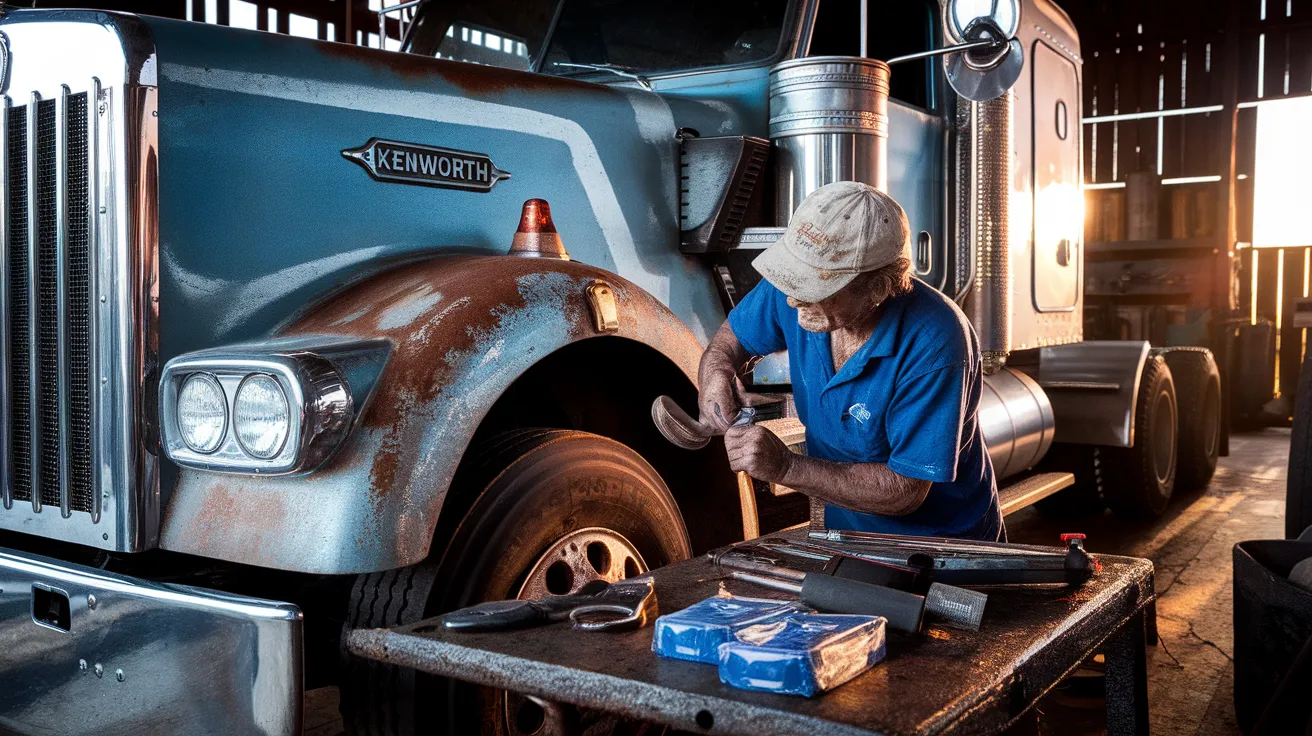
Main Insights
Grasping the Critical Role of Routine Truck and Fleet Maintenance
While it may appear challenging, understanding proper fleet and truck maintenance is vital for every prosperous company. The benefits of maintenance greatly surpass the resources you put in. Regular checks and servicing can significantly extend your fleet's service life, avoiding hefty replacement costs. Moreover, there's an obvious relationship between regularly maintained fleet and better fuel economy. This means reduced gas expenses, boosting your bottom-line performance. Moreover, regular upkeep can help identify minor concerns before they escalate into major ones, preventing costly repairs later on. Thus, never discount the importance of regular upkeep; it can be a significant factor for your company's profitability.
Examining Essential Elements of a Effective Maintenance Framework
To ensure your fleet's performance and lifespan, it's critical to recognize the key components of a well-designed maintenance program. You'll need to understand the basic principles of maintenance, monitor the health of your fleet consistently, and put in place preventive measures in advance. With these implemented, you're ready to reducing downtime and optimizing productivity.
Critical System Maintenance Features
If you aim to boost your fleet's efficiency and lifespan, implementing a robust maintenance program is crucial. Key components of the program include scheduled inspections, regular servicing, and preventive repairs. Every component is essential in avoiding costly breakdowns and decreasing downtime. While the rewards of a maintenance program are significant, it's important to address the setup hurdles. These often involve resource constraints and employee pushback. Yet, with proper planning, clear communication, and dedication to training, these barriers can be addressed. Don't forget that an successful maintenance program isn't just about repairs; it stops them from occurring. It's an commitment in your fleet's future – and it's one that will yield significant returns.
Fleet Condition Monitoring
When examining the fundamentals of a successful maintenance program, acknowledging the importance of fleet condition monitoring here takes center stage. It extends beyond ensuring vehicle functionality, it focuses on optimizing fleet performance. Fleet monitoring systems offer a thorough view of your fleet's health, allowing you to detect potential issues before they escalate.
These monitoring systems measure vital parameters like fuel efficiency, tire health, engine performance, and more. Through analyzing this data, you're not just guaranteeing the lifespan of your fleet but also minimizing unnecessary repair costs. Keep in mind proactive identification is key in fleet management. So, adopt trustworthy monitoring technologies and stay ahead of the curve. Don't merely address problems, forecast them. Monitor your fleet's status regularly and your operation will operate efficiently.
Implementing Preventive Measures
Although tracking your fleet's condition is crucial, putting preventive strategies in place is just as crucial to maintain a effective maintenance program. You must spot potential concerns before they escalate into costly repairs or downtime. So, let's talk preventive measures.
A key strategy is creating a thorough maintenance checklist. This document should specify all required checks, maintenance procedures, and replacements. Periodic engine checks, tire servicing, and oil changes are a given. But don't overlook smaller components like windshield wipers, lighting systems, and filter components.
Your maintenance plan needs to include a schedule for each task. Sticking to this timeline ensures that your fleet maintains optimal performance. Remember, preventive measures saves expenses, time, and problems in the long run.
Essential Routine Checks for Truck and Fleet Maintenance
To guarantee your vehicles continue to be in optimal condition, you need to focus on regular maintenance inspections. These checks include routine maintenance checks and essential system reviews. By maintaining these essential protocols, you'll increase your fleet's lifespan, enhance operational efficiency, and consequently, minimize major repair expenses.
Routine Equipment Inspections
Regular maintenance inspections are your strongest line of defense from unplanned vehicle and fleet malfunctions. This maintenance gives you an opportunity to spot and address issues before they escalate into serious accidents or expensive repairs. One of the most significant scheduled maintenance benefits is the prevention of downtime, which can substantially influence your operation's performance and revenue.
Essential Component Inspections
Following up on the critical nature of scheduled maintenance inspections, let's explore the specific essential component checks that should be conducted regularly to maintain maximum truck and fleet performance. Start with the brake system – verify all components are working properly, from brake pads to fluid levels, while also checking for leaks. Neglected, brakes could fail, leading to serious incidents. Tire pressure checks are equally crucial. Underinflation raises fuel consumption and tire wear, while overinflation can cause a blowout. Obtain a high-quality pressure gauge for accurate readings. Remember tires should be cold during checks for best results. Routinely carrying out these essential checks can help avoid costly repairs and potential accidents. Stay safe on the road.
Essential Fleet Maintenance Practices for Peak Performance
While overseeing a fleet, it's vital that you focus on preventative maintenance to maintain peak efficiency. Setting up a systematic preventative scheduling system is key. This prevents unnecessary wear and tear, and reduces the chances of unscheduled downtime. You need to plan regular checks and servicing based on mileage, time, engine hours, or fuel used. Remember each vehicle is unique and may require a personalized approach.
Maintenance education serves as another vital strategy to secure peak efficiency. Provide your staff with the essential skills to detect potential issues before they escalate. This reduces downtime but also reduces costs. The combination of preventative scheduling and maintenance training will result in a highly effective and trustworthy fleet. Prevention is always better than cure.
Crucial Pointers for Commercial Vehicle Upkeep and Renovation
Even though fleet and truck maintenance and restoration might appear challenging, grasping the fundamentals makes it easier. The first thing you should do needs to be to learn about various repair techniques. This understanding will enable you to diagnose issues effectively and promptly. Next, arrange maintenance work according to how serious the issues are and the vehicle's role in your operation. Regularly inspect all units for potential issues and fix them immediately to avoid additional problems. Remember, restoration isn't just about fixing issues, it's focused on enhancing the vehicle's functionality and longevity. Lastly, consistently choose premium components for repairs; they'll provide better durability and performance. Follow these principles, and you'll navigate vehicle fleet repairs and upkeep successfully.
Maximizing Sector Developments for Cutting-Edge Fleet Operations
To maintain a competitive edge in the trucking industry, it's essential to harness industry innovations for improved fleet maintenance. New technologies are revolutionizing the maintenance landscape. Make use of data analytics to analyze your fleet's performance and anticipate potential issues before they occur.
State-of-the-art monitoring systems can track and monitor engine performance and health, fuel usage, and driving habits. Leverage this valuable information to implement predictive maintenance, minimizing costly operational interruptions.
Never ignore software updates. Such updates commonly include critical updates and fixes that enhance your automotive fleet's reliability and protection. Keep in mind managing your vehicles isn't limited to routine maintenance. You're operating in a tech-focused period, and keeping up with industry innovations will safeguard your fleet's durability and success. With appropriate procedures, you will decrease time and money, and safeguard human life.
Popular Questions
What Requirements Must a Skilled Fleet Service Technician?
You will require a proper certification, fulfilling the standards of an accredited mechanic institution. Additionally, you'll need a comprehensive skill assessment, demonstrating your competency in various aspects of fleet maintenance and repair. Experience counts too!
How Often Should Fleet Vehicle Tires Be Replaced?
Similar to clockwork with the changing seasons, you need to examine your fleet's tire wear regularly. However, it's typically best to install new tires every three to 6 years, based on road conditions and usage patterns.
What Are the Warning Signs of Truck Engine Problems?
You'll notice truck engine problems via symptoms like strange engine sounds or reduced fuel economy. Additional indicators are heavy smoke emissions, fluid leakage, along with a check engine light that won't turn off.
How Does Technology Impact Truck and Fleet Maintenance?
Technology is fundamental in optimizing truck maintenance. Modern sensors supply real-time data, while analytical tools forecast issues before they occur. You'll notice less vehicle downtime, enhanced security and ultimately, cost savings. It's a game-changer.
How Do Maintenance Needs Vary Across Fleet Vehicle Types?
Various vehicles need distinct maintenance schedules. You need to consider the intended use, weight limits, and terrain type, as these elements greatly influence the necessary maintenance. Always adjust maintenance according to the vehicle classification.
Conclusion
At the core, the key is ensuring your fleet operates efficiently, isn't it? Routine maintenance isn't merely a recommendation, it's essential. By pinpointing crucial elements, performing regular inspections, applying preventive maintenance approaches, and leveraging technological advances, you're not just maintaining your trucks, you're developing a high-performance fleet. And keep in mind, truck and fleet repair isn't a failure, it's a pathway to enhancement. Stick with it, and you'll witness your fleet's productivity, consistency, and lifespan reach new heights.